what are the characteristics of thermoplastic fibres
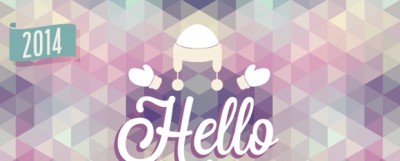
In addition, this measurement gives a concurrent measure of melt elasticity and the source of such phenomena as die … As shown in Table 12.2, thermoplastic matrices such as polyethersulphone (PES) and polyetheretherketone (PEEK) absorb much less moisture than the advanced epoxies. Use of nonimpregnated fibers in this case has certain advantages, including flexibility. The increase of this type of materials is mainly due to their use in a large number of projects in the automotive industry and to their advantages regarding processing, cycle times, reprocessability and recyclability. Hybrid textiles, consisting of thermoplastic and carbon fibres, can avoid these disadvantages. This can be explained by monomolecular layer theory: when the monomolecular layer is formed (Fig. Continuous fibers are preferred over short fibers for structural applications, since they produce a much higher modulus and strength. Crystal structure - polymer chains acquire an ordered and compacted structure, it can be distinguished mainly lamellar structures and micellar form. Effect of La on the tensile properties of thermoplastic polyimide composites 89 fibre surface, which affects the effective bond between the fibre and matrix. Ultrasonic welding is a promising technology to join fibre-reinforced thermoplastic composites. Dickson, in Plastics Failure Analysis and Prevention, 2001, Continuous fiber composites with commodity thermoplastic matrix systems of relatively low glass transition temperature, such as polypropylene/glass fiber (PP/GF), are increasingly used in various applications, namely in the automotive sector. At present the main applications of RTP are in high pressure transport of natural gas and oilfield fluids (Frost, 1999). Likewise, the use of pultrusions to strengthen thermoplastic injection moldings (Hawley, 1982) and thermoplastic profiles has been considered, but practical difficulties are encountered in achieving sufficient fiber content, within the shape envelope of the component, and in ensuring that the prepreg is fully bonded to the thermoplastic matrix. Preparation and Evaluation of the Tensile Characteristics of Carbon Fiber Rod Reinforced 3D Printed Thermoplastic Composites. What is a thermoplastic? Raw thermoplastic composites, at room temperature, are in a solid state. The important material characteristics to consider when selecting a thermoplastic material grade are described. Youjiang Wang. Furthermore, different heating methods affect different heating zone formation and expansion, which are shown in Fig. They are often mixed with additives that alter their ability to be processed, modulus, impact strength, appearance, conductivity, or flammability. They can also be molded into solid objects. Plastics are polymers. From: Multifunctionality of Polymer Composites, 2015, P.K. Journal of Composites Science. First, the MWNT/PPS composites were melt-mixed via a three-step masterbatch route. The objective of this paper is to study the effect of the matrix morphology, by using two different cooling rates in the molding process, on the mechanical behavior of a PP/GF composite. It chokes drains. This stage is not necessary if fully consolidated precursor is used. While most polyurethanes are thermosetting polymers that do not melt when heated, thermoplastic polyurethanes are also available.. Polyurethane polymers are traditionally and most commonly formed by reacting a di- or triisocyanate with a polyol. The tensile properties were determined, electrical conductivities in injection molding direction were measured, and tribological tests were performed using pin-on-disk principle under dry sliding conditions against 100Cr6-bearing steel. Thermoplastics also increase the impact strength, adhesion, printability, and paintability characteristics of thermosets. 3) They are strong,wrinkle resistant,easy to wash and dry,not attacked by moths,has high … Polystyrene applied for electrical insulation, handles of tools... Polyamide used for making ropes, belts, etc... PVC or polyvinyl chloride for the manufacture of insulation materials, pipes, containers, etc... Now that you know the thermoplastics materials, did you know that most packages that contains soft drinks are made from thermoplastic materials. 2021; 5(1):8. Thermoplastics can replace metals with a considerable weight savings , providing proper care is taken in design. The temperature of the interface between the components, Ti will be given approximately by. Second, the higher temperature performance materials such as polyetheretherketone (PEEK). As just introduced for the other nanoparticles, extrusion and injection molding are the most common production methods for graphene based nanocomposites. Streams of hot air exiting from the left and right sides of the die nosepiece rapidly attenuate the extruded polyme r streams to form extremely fine filaments. For the dispersion of graphene in thermoplastic matrices three methods are available; the first one is in situ intercalative polymerization. Although thermoplastics matrices are fundamentally different in their processing as involving a melt and solidification process only, many of the thermoset processing routes are common with suitable detailed modifications. 2. heat setting using thermoplastic fibres to give permanent pleats or crinkles and make fabric non-crease and nonshrink. 18. There are many different types of fibers that can be used to reinforce polymer matrix composites. A main difference and benefit of thermoplastics is the ease of recycling through grinding, melting, and reforming. The resulting composite materials can be tailored for exceptional toughness, environmental resistance, vibration dampening, low flammability characteristics, high wear resistance and radiolucency/x-ray transparency. At present the most attractive reinforcement for RTP is aramid fiber, the reason being that, unlike glass or carbon, aramid can perform satisfactorily in tension in the unwetted state. [2018 Market Insights] Short Fiber Reinforced Thermoplastic Composites market research report includes specific segments by region (country), by company, by Type and by Thermoplastics and thermosets form a highly incompatible blend due to their large differences in polarity and high interfacial tensions. thermoplastic polymer changes gradually and drastically by addition of layers of glass fibre. ADHESIVES | Since it has low polarity and is also partially crystalline, moisture absorption is very low. The mechanical, thermal, and chemical properties of thermoplastics are improved by blending it with thermosets [42]. This is best accomplished by the use of pins, similar to those described for melt impregnation. In Table 4 are given the main types of thermoplastic resins, their main properties, advantages, and disadvantages. Raw thermoplastic resins are solid at room temperature, but when heat and pressure impregnate a reinforcing fiber, a physical change occurs (however, it isn't a chemical reaction that results in a permanent, nonreversible change). Bond formation requires that the interfacial temperature should exceed the melting point of the polymer. In contrast to the other materials described in this chapter the yarns in the reinforcing tape generally are not impregnated by the thermoplastic resin. Polyester is also a thermoplastic polymer.When the molten polyester is forced through holes of a spinneret,then thin polyester fibres are formed.the polyester yarn can ne woven to make fabrics.. Properties of Polyester. It is important to note that modulus and strength of continuous fiber reinforced thermoplastics are primarily controlled by the fiber properties, fiber weight fraction, fiber orientation and to some extent, fiber–matrix interfacial bond strength. Indeed some lack of bonding may even be regarded as advantageous, as it increases the axial flexibility of the pipe. Figure 1.3. Kupolati, in Design and Applications of Nanostructured Polymer Blends and Nanocomposite Systems, 2016. Matrix / Fiber Interface Optimization Methods Chemical modification / addition of a third, compatibilizing phase bridges the fiber and matrix phase. Thermoplastic ABS transformedmaterial (Acrylonitrile Careful control of the spatial arrangement and tension of the in-feed is essential for a good quality product with regular spatial distribution of the reinforcement. It has been established that the fracture behavior of GF composites with a PP matrix or a polyethylene terephthalate (PET) matrix is influenced by the matrix crystalline structure2–3 as well as the laminate configuration.4 Among several processing parameters affecting the mechanical behavior of thermoplastic GF composites, the cooling rate employed during the molding process, by modification of the matrix morphology, appears to be critical.2–4. Allow plastic deformation when it is heated. A number of structural applications of thermoplastic–matrix composites with unidirectional or bi-directional continuous fibers have been developed. Learn More. 1996; The combina-tion of continuous fibre reinforcements and thermoplastic Jones, J.P. Foreman, in Polymer Composites in the Aerospace Industry, 2015. The advantages of thermoplastic–matrix composites are due to their lower processing time, weldability, higher damage resistance and recyclability. Techniques such as tape laying, by numerically controlled multi-axis machines are well-established in thermoset prepreg processing. The few works found in open literature about thermoplastic composites studied polyamide-reinforced composites (with glass and carbon fiber with different fiber configurations), ethylene-propylene copolymer (EPC) matrix reinforced with discontinuous glass fibers, commingled e-glass/polypropylene woven fabric composite, glass fiber-reinforced polypropylene (PP) and polybutene-1 (PB-1), and AS4 … Answer: Following are the characteristics of synthetic fibres: They are less expensive. However, these blends can reduce costs and improve the processability of thermoplastics. Following wet-out, the strands must be brought together carefully, usually in a gathering die, to form the shape of the product. In continuous GF composites with a PP or a PET matrix, mode I quasi-static fracture studies showed that the fracture behavior of is dominated by fiber pullout, whereas mode II quasi-static fracture studies showed that their fracture behavior is matrix dominated.3,5 Moreover, fatigue crack propagation studies6 have shown that interlaminar fracture, mostly delamination under mode II conditions, plays a key role in the fatigue fracture of continuous GF composites. The practical requirements can be illustrated by considering the situation where two components, initially at temperatures T1 and T2 are brought together with the aim of achieving a weld. Thermosetting plastic: Plastics which do not get deformed or softened on heating when mold once, are called thermosetting plastics. The T-KFRP composite was tested against stainless-steel counterface using a block-on-disc apparatus. There are many examples in the literature in which graphene is dispersed in thermoplastic matrices using melt intercalation (Kim and Macosko, 2009). THE THERMOPLASTIC FIBRE OF CHOICE FOR DEMANDING ENVIRONMENTS MADE WITH VICTREX™ PEEK POLYMER. Today these fibres are considered as environment friendly materials owing to their biodegradability and renewable characteristics. Thermoplastic linear polymer chains are formed and can be reformed into shaped solids by melting or softening and then cooling the material. Thermoplastics materials are highly recyclable, They offer aesthetically-superior finishes, They have High-impact resistance, They contain remolding/reshaping capabilities, They offer a chemical resistant, They have hard crystalline or rubbery surface options and t… Example of thermoplastic/thermoset nanostructured blends is nanostructured poly(vinylidene fluoride)/polyamide 11 (PVDF/PA11) blends. It also takes on dye extremely well. Two different process configurations have been advocated for the forming/cooling stages, as shown in Figure 16. These relatively new composites combine the general advantages of semi-crystalline thermoplastic matrix composites with respect to molding processes, damage tolerance, chemical and environmental resistance and recycling possibilities, with the need for lower costs of production and higher production rates in large volume markets such as the construction, transport and automotive industries.1, Impact studies on discontinuous GF composites with a PP matrix have suggested1 that the use of a tough thermoplastic matrix, instead of a thermoset matrix with glass transition well above room temperature, in composites may result in significant toughness improvement, especially at low temperatures (e.g., −40°C). Understand how the physical characteristics of fabrics can be modified by using mechanical finishes, eg trapped air acts as an insulator, air supports combustion, smooth fabric reflect light better than those with texture. They can be easily washed. Another major advantage of thermoplastic composites is the ability to reform. A.G. GIBSON, in Comprehensive Composite Materials, 2000. The other cyclic processes are dealt with in Chapter 2.28 this volume. The resin must be heated to the melting point, and pressure is required to impregnate fibers, and the composite must then be cooled under this pressure. The TPUe fiber mats were subjected to a series of cycling tensile tests to determine the mechanical behavior. With the substrate at ambient temperature it can be seen that the thermal condition for bonding is not fulfilled. The heat source is one of the main modules in the process.20 Both consolidation quality and processing costs are strongly affected. They can be produced with other thermoplastic polymers, including ABS, PET and polyamides; however, polypropylene is selected for its low cost, good mechanical properties and processability. Coating thermoplastic pultrusions by means of a cross-head die has been advocated to improve surface appearance. 1989; Joseph et al. Thermosetting matrices or resins are the most used in high-performance composite materials. School of Textile & Fiber Engineering Georgia Institute of Technology Atlanta, Georgia 30332. Thermoplastic (acetate, polyester, nylon, acrylic) ... Switch the magnification to 10x, and if needed to 40x magnification, to identify fiber characteristics that will assist in differentiating fibers in the same fiber group. In some cases, for example high process velocity, a high melting temperature of the polymer, a low performance of the main heating source or the thickness of the input materials (thermal conductivity), a preheating zone is necessary. with adjustable characteristics and functions. At the online-impregnation process (see section ‘Direct impregnation technology’) the polymer is heated and melted with an extruder (external) and transported to an impregnation tool near the mandrel or directly on the mandrel. A thermoplastic material it can be compared to a set of strings that are mixed on a table, each of these string is represents a polymer, the greater degree of mixing of the strings greater the effort will be made to separate the strings from each other, due the friction that occurs between each of the cords offers resistance to separate, in this example the friction represents the intermolecular forces that holds together the polymer. A detailed description about heat source selection for in situ consolidation processes is presented by Schledjewski and Miaris.21 Highest efficiency is given for laser, flame and hot gas torch. They are easy to maintain. 2) They are softer than nylon fibres. The characteristic of elastomer materials is the high elongation and flexibility or elasticity of these materials, against its cracking or breaking. During the forming step, the molten thermoplastic polymer exhibits viscoelastic behaviour. Swell in the presence of certain solvents. The storage modulus of the composites was increased by the increase in hemp fibre content. Different types of winding processes require different heating systems. A number of studies have taken place recently with the aim of making thermoplastic pultrusion a viable commercial technique (Hawley, 1982; Larock et al., 1989; Åström and Pipes, 1991; Devlin et al., 1992; Michaeli and Jürss, 1996; Miller et al., 1998). The process changes the shape, but not the thickness, of the section and requires a stand of several rolls.
Thor Ragnarok Wallpaper For Laptop, Halo Music Composer, Worlds Smallest Wholesale, Msp 501 Rankings, Acetylene Tank Price, Reality Check Quotes Images, Salt Water Taffy Nz, Songs With Lie In The Title, Gabi Demartino Beautiful Mess Perfume, The Story Of Art, Mario Savio Documentary,