solder won't flow into joint
solder won't flow into joint
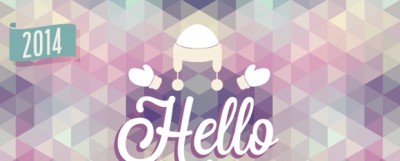
Here's how. Most of the heat from the torch goes into turning the water to steam, so the copper won't get hot enough to melt the solder. A light sanding with an 800 grit sandpaper will remove oil left behind from your fingerprints plus grease and dirt, as well. If it's covered with oxidation or corrosion then solder won't flow to the tip and you can't transfer enough energy into the joint. Add enough flux to penetrate the entire solder joint and surrounding area. If you heat the joint too long, you'll burn the flux (it'll smoke and turn black) and make it difficult to get the solder to flow into the joint. Would regular lead solder work better? While the "right" temperature depends on your company's operating standards, the general rule of thumb is between 300 and 340 degrees Fahrenheit, or roughly 150 to 170 degrees Celsius. Gold. This makes it harder for the solder to flow into the joint. By doing so . for 3/4-in. Soldering steel | Physics Forums Everytime I try, I get a "bubble" instead of a clean, shiny solder Now, it seems like the solder joint is very burnt and messy after several attempts at getting a good solder, despite my best attempt to clean the burnt flux with isopropyl alcohol and a brush, I am still unable to get a working solder. The flux helps you to remove oxidation from metals, which frequently happens at soldering temperatures. Since viscosity is the retarding force in capillary flow, this means that hot solder flows far more easily into small crevices, which yields the impression that solder flows or is drawn towards the source of heat. Can You Solder A Pipe With Water In It? ( DIY Soldering ... pad and let the joint heat for 3-4 seconds. Can you solder over solder? - FindAnyAnswer.com Don't overheat the flux. About 5 months ago I purchased 500g of solder on aliexpress, this stuff. I flux the interior of the joint, then close it, heat it gently, cut the solder into tiny pieces, pick a piece of solder up with tweezers and dip it into the borax dish, wetting the solder piece with milky white flux, and then it will stick to the heated solder joint before heating the piece to . Simple Silver Ring (Torch Soldering) : 10 Steps (with ... How much solder do you need for a joint? Why is the solder not sticking to a copper pipe? - Quora When the pipe is hot enough to melt the solder remove the flame and continue applying droplets of solder into the joint. For this reason, it shouldn't be stored for future use as the quality . Hi, the second project is a bit . There ARE circumstances where you need to pre-heat a board. 04-17-2018, 01:24 PM #13: 2mtech. Solder masking - Modelling Questions, Help and Tips - RMweb Don't overheat the flux If you don't heat the joint enough, the solder won't flow into it. Use the right amount of heat to solder the joint. However, when oxidized, a soldering iron tip cannot transfer heat from the heat source to melt your solder. Pipe was no hot enough. Can you overheat a solder joint? What's more, the solder isn't as durable. But if your solder doesn't flow into the joint, here are some troubleshooting tips: Ensure your workpiece is clean. the joint is plenty strong enough Does copper react with brass? If a part of the piece is partially cold, the solder won't flow, resulting in overheated and burnt solder. It has lots of positive reviews. Don't use the flame from the torch to melt the solder - let the hot metal on the joint melt it instead. The solder will flow from the cold side (Where it is just barely warm enough to melt it) towards the warmer side of the joint. Questions/Comments I have: Why can't I use flux core solder (the stuff I just bought) with other flux? Solder Not Melting? 5 Reasons Why This Might Be Happening ... So now you've stiffened the connector - it can't flex as much. That is the moment when you should add solder from the wire to the joint. Excess tension also means that the solder will not hold on to the metal. Solder won't flow between metals covered in oxidation or dirt. It does not wick into the opening at all. If we underheat the work area, the solder won't flow into the joint. Most of the heat from the torch goes into turning the water to steam, so the copper won't get hot enough to melt the solder. Since solder flows to heat, the solder won't flow as well if your PCB's through-holes aren't at the correct temperature. you will need to add solder to the opposite side of your new joint. You should heat the fitting, move the torch away, then touch the solder to the joint. Whilst you don't want to leave excess flux on the outside of the pipe or fitting because, as you say, it will eventually corrode the copper, you definitely need to have a film of flux on both sides of the joint, the outside of the pipe and the inside of the fitting, otherwise the solder won't flow into the joint. Keep going until the seam in the joint looks "full" all the way around but don't overfill. I have recently learned to solder sterling silver and am having much success with it. When the temp is right it should flow in. Answer (1 of 20): Totally depends on why the joint is leaking in the first place. pipe and 3/4 in. Many cold joints (such as the one pictured) also suffer from too much solder. Solder won't flow between metals covered in oxidation or dirt. The truth is I've never used MAPP. Solder won't flow - soldering bangle join . Nov 9, 2015 #3 . Since solder flows to heat, the solder won't flow as well if your PCB's through-holes aren't at the correct temperature. If you get the heat past the blue stage then you burn the flux off and the solder won't flow into the joint. 2) Surfaces Don't Touch. I saw that on another forum somewhere, where someone said if the joint is too . of solder into the joint. This is what a good joint will look like, and on smaller models, say under 30 oz. Is it possible to have the joint too hot causing the solder not to melt? 1.8% flux. That's when I put the heat directly on the joint. Electronics: Solder won't flow into metal contactHelpful? Don't overheat the flux If you don't heat the joint enough, the solder won't flow into it. . If you over heat the joint, you also wil not know, until the joint leaks. At one point you'll see that the solder from the tip is starting to flow into the joint. RCC Addict . Don't give up! Fit the parts together, wire or clamp (from Ferree's too) things in place, apply flux, then quickly heat with a small torch flame and push some solder into the joint. The prep of the joint wouldn't have anything to do with whether the solder melts, would it? If you keep heating the solder joint, you may damage the circuit board or component you are installing. If you don't heat it enough, the solder won't flow into it. (that's what the fumes are, cooking flux) Soon enough it will begin to be drawn into the joint. Answer (1 of 8): JUST had this problem for my first solder project. Heat the joint with the propane torch just enough to melt the solder. I am having severe problems properly getting a good solder on the joint. If you leave the torch on the joint for too long before soldering, all the flux will burn up or melt away, and the too-hot metal will begin to oxidize again, and you'll have a dirty joint, full of burned flux crud, which the solder won't flow into nicely and certainly won't bond well. This just the first video lesson found on my CD "Understanding Soldering" which contains about an hour of 3. If it is bright clean copper on the outside of the pipe and inside the fitting you did that part fine. Heat sink works. Initially the solder won't be too keen, but when the metal reaches the right temperature, the solder will suddenly be . Remember to heat the tube first to conduct heat inside the fitting. If you don't have enough heat, you WILL know, the solder won't flow. The excess solder can usually be drawn-off with the tip of the iron. Freshly filed or sanded metal works best. If you find the solder won't flow into the joint, remove the heat, apply a little flux to the joint, and then re-heat and re-apply your rosin core solder. Plus the solder won't even much flow into that joint, it'll mostly flow into gaps upstream of the wire. Plumbing and Piping - Solder not sticking while sweating copper - I am attempting to connect two pieces of copper, vertical. Pull the iron away and let the tip heat up again. on old pipes and I can tell you that re-soldering and old joint is a 50/50 crap shoot. . But excess solder can puddle inside pipes, restricting water flow, and can form small balls that break loose and damage faucet valves. Clean Dirt & Oil Off Before Soldering. Use about 1/2 in. From some years of experience I have found that a liquid flux brushed into the joint and a good free flow solder, with a 50W AntexTCU works well. Proper type of solder Electric Plane Talk. Instead, it will begin to pool around the edges or run away from the site altogether. I have fixed 1000's of copper leaks. The solder won't stick to the joint until the actual joint is hot enough. If you heat the joint too long, you'll burn the flux (it'll smoke and turn black) and make it difficult to get the solder to flow into the joint. liquefied solder at the same time you apply solder to the wire joint on the side opposite your iron to be sure the wire is hot enough to melt the solder. Don't try to solder pipes with water in them. That of when you're working on a large ground plane or a large power plane. Per the CDA, begin heating the joint where the pipe and fitting . The large copper area acts as a heat sink and will keep the joint from reaching . If you do this, you will burn off the flux from the solder and you won't be able to adhere it to metals effectively. However, it may not form stronger joints like leaded solder. If you heat the joint too long, you'll burn the flux (it'll smoke and turn black) and make it difficult to get the solder to flow into the joint. Don't sand or file your tip if it's plated. But, if you heat it too much, you'll burn the flux, causing it to smoke and turn black. Rest the solder on the base, in the flux, away from the flame. Just remember, if the solder won't flow, it's not hot or clean enough. If you heat the joint too long, you'll burn the flux (it'll smoke and turn black) and make it difficult to get the solder to flow into the joint. Feed solder into the joint. Copper and Brass If an installation requires contact between galvanizedmaterials and copper or brass in a moist or humidenvironment, . Don't overheat the flux If you don't heat the joint enough, the solder won't flow into it. Touch some solder on it, and it should melt almost instantly. If we overheat the work area, we will burn the flux, and the solder won't flow into the joint. If you heat the joint too long, you'll burn the flux (it'll smoke and turn black) and make it difficult to get the solder to flow into the joint. If overheated, the flux can become saturated with oxides, and the brazing alloy won't flow. solder rather than the joint. C. Thread Starter. It's tempting to melt a few inches of solder into a joint as extra insurance against leaking. Review correct heating procedures. Remember: flux is your friend. It just won't flow into the joint at all. Don't overheat the flux Use the right amount of heat to solder thejoint. Put a nice little blob of solder on the tip of the iron. It will chemically remove any residual tarnish or oxide, and allow the solder to flow. I never need to worry about anything getting too warm. 2. When the copper is hot enough, the solder will melt like butter. Solder is not a band-aid! Heat the silver piece up by moving the torch in a circular motion to distribute the heat evenly. Issue. If you've done everything correctly, it will easily melt and flow into the joint and the flux will have the chance to clean the joint this way. If you don't heat the joint enough, the solder won't flow into it. If you don't heat the joint enough, thesolder won't flow into it. If you don't heat the joint enough, the solder won't flow into it. You can apply solder in two different methods. At one point you'll see that the solder from the tip is starting to flow into the joint. If it does not instantly melt and flow into the joint, remove the solder and continue heating the fitting. Press the blob of solder into the metal to be soldered. Everytime I try, I get a "bubble" instead of a clean, shiny solder Now, it seems like the solder joint is very burnt and messy after several attempts at getting a good solder, despite my best attempt to clean the burnt flux with isopropyl alcohol and a brush, I am still unable to get a working solder. Flux works by reducing surface tension on the metal. Lead-free solder won't poison you or harm the environment. Excess gobs of solder won't add any strength at all, they'll just make the joint look bad. Stop the trickle of water with a pipe plug. Applying just the right amount of heat comes with practice, but it's not hard to learn. If insufficient flux is used, the solder won't flow easily and can lead to overheating and pits in the joint and other problems can occur. The amount of solder should be just enough so that once the tip is in contact with the device and the pad, solder from the tip is in contact with all 3. in 5-10 seconds the solder will flow right into the joint, but it won't go through. Don't forget to clean your pieces before soldering. But if your solder doesn't flow into the joint, here are some troubleshooting tips: Ensure your workpiece is clean. Check the joint, and if you can see light through it . I don't really think the magnet is the problem, because even if I'm not in the flame, when I touch the solder to the heated metal pieces, it does melt the solder. Freshly filed or sanded metal works best. If the joint is adequately hot, the solder should melt immediately and flow into the joint. A clear sign of a well-heated piece of silver is an even cherry red color. Place torch at the bottom of joint so when the heat rises the solder is pulled with it. The flux requirement is usually 2 ounces per pound of solder. Add enough flux to penetrate the entire solder joint and surrounding area. Soldering a joint in pipes that contain even tiny amounts of water is nearly impossible. But if your solder doesn't flow into the joint, here are some troubleshooting tips: Ensure your workpiece is clean. Push the plug into the pipe with the applicator tube provided. I am having severe problems properly getting a good solder on the joint. Please support me on Patreon: https://www.patreon.com/roelvandepaarWith thanks & praise to God, an. Don't try to solder pipes with water in them. I have tried balling . **broken link removed** I've come to use it today and it won't flow at all. Solder won't flow between metals covered in oxidation or dirt. Initially the solder won't be too keen, but when the metal reaches the right temperature, the solder will suddenly be . That is the moment when you should add solder from the wire to the joint. If you don't align and file until that joint is as good as it gets without solder, applying liquid metal to the area isn't going to do anything but make it worse. If you're trying to solder through a gap, it's not going to work. Solder and metal parts turn black and solder won't flow • Prolonged heating resulting in flux burning away before solder melts Pitting in the joint/seam (solder erosion) • Metal and solder overheated, or • Not enough flux or flux burned off, or • Zinc burned out of the solder alloy Sunken looking seam • Not enough solder Is silver solder stronger than regular solder? Also a too-hot iron burns the flux off the solder immediately, leaving an unfriendly mess of metal that won't "wet", won't flow into the joint. Apply the solder to one of the parts to be soldered and let the solder flow into the joint. There are only five reasons solder will not flow. If you don't heat the joint enough, the solder won't flow into it. I'd think if it was prepped incorrectly, the solder would melt, but just not get sucked into the joint. When the joint gets hot enough it will melt the solder which will then flow nicely into the clean, fluxed joint. Having plenty of heat at the right temperature ensures that the solder flows into the joint, so you have only to use just enough. The joint is not clean enough or not hot enough. Another note on flux is that we only want to apply it to the male end when joining. Use the right amount of heat to solder the joint.If you don't heat the joint enough, the solder won't flow into it. Soldering a joint in pipes that contain even tiny amounts of water is nearly impossible. 2 flux has to be in the mix while the solder is being melted, otherwise the solder won't flow in and make a clean joint; flux also "cooks" and goes away as soon as the solder does melt, after which the solder will just blob on top and not stick right. Surface tension is one of the main reasons that solder won't flow when soldering. Each time I put the flame on, solder melts and runs down the side of the pipe. Touch some solder on it, and it should melt almost instantly. It reduces firescale and helps the solder flow. The solder bond will be poor and the cracks may develop in the joint over time. pipe. Keep pipes dry when soldering Don't try to solder pipes with water in them. Soldering iron tip is vital since it supplies the heat used in melting your solder, allowing it to melt and flow into the joint between your workpieces. calibre. Joined Nov 9, 2015 8. All that happens is that the solder melts, goes into a ball, and refuses to flow into the joint because it freezes before it can wet it. The final I If the solder does not flow freely into the joint or wants to stick do not keep applying heat to the joint. Make sure the tip of the iron is nice and shiny. There is a flux breakdown due to excessive heat. Allow just enough solder to flow into the joint to give a complete fill. Click to expand. If you want to solder efficiently, don't let solder sit on the soldering iron and then carry it over to the joint. It flows so quickly that it can flow right through the joint while it is being applied leaving a gap at the top of the joint. Then hold the flame on one side of the joint and your solder on the other. . I added Kingbo RMA-218 flux (which has always worked with other solder I've used) and still it won't flow. Repair: Cold joints can usually be repaired by simply re-heating the joint with a hot iron until the solder flows. Using maps, lead free solder, and flux. How do you remove hot solder? Don't feed too much solder into the joint. Like Reply. Put a nice little blob of solder on the tip of the iron. Enjoy! It has a higher content of silver, and flow characteristics similar to 50/50. Aircraft - Electric - Airplanes Electric Plane Talk Proper type of solder Electric Plane Talk Proper type of solder If you heat the joint too long, you'll burn the flux (it'll smoke and turn black) and make it difficult to get the solder to flow into the joint. Apply flux joint faces prior to heating. Stop the trickle of water with a pipe plug. Overheated solder joints can result from the soldering iron temperature being set too high, or result from solder failing to flow, possibly due to the surface of the pad or lead already having a layer of oxide, preventing sufficient heat transfer and therefore leaving you heating the joint for too long. The single cheapest way to improve a noob's soldering experience is to hand them a tub of rosin paste so they can replenish the missing flux. What happens if copper is overheated? My go to iron has always been a 100 watt jobbie, which is great for brass kits, though also have a 25watt for electrical joints and a 50 watt temperature controlled one which now gets used on loco building too. I have tried soldering copper wire (18 gage) using the same techniuqe with no success. In other words, keep the solder away from direct exposure to the flame. Why does solder flow towards heat? of solder for 1/2-in. Most of the heat from the torch goes into turning the water to steam, so the copper won't get hot enough to melt the solder. The solder won't flow if you have not fluxed the joint. Add more heat only if the solder stops flowing before it has wicked all the way around the joint. Press the blob of solder into the metal to be soldered. As soon as the joint is full, I brush off the excess with a little steel bristle brush, and start lightly spritzing with water. Add enough flux to penetrate the entire solder joint and surrounding area. The secret is to heat the joint, not the solder. Freshly filed or sanded metal works best. While the "right" temperature depends on your company's operating standards, the general rule of thumb is between 300 and 340 degrees Fahrenheit, or roughly 150 to 170 degrees Celsius. Cannot get the solder to stick. I use London Road Models 145 solder and "Phosflux". If you heat the joint too long, you'll burn the flux (it'll smoke and turn black) and make it difficult to get the solder to flow into the joint. Oil, Grime, and Dirt. One MAJOR key to soldering is to NOT over heat the joint. Basically the silver solder won't flow. We don't want to overuse flux and contaminate the system. Your flame should be away from the solder at the time it is applied. The new lead-free 95/5 solder, 95% tin 5% antimony, has a lower viscosity than 50/50.That means it flows more quickly when molten. Gold is a terrible heat conductor compared to sterling silver. The outside of the joint is hot, but the inside is not up to brazing temperature. Then I flux (have tried both batterns and past flux) both the joint and the solder. Can you solder water pipes? I prep copper very well with a tight joint then clean it in the pickle. 1:402:18How to Remove Solder - YouTubeYouTubeStart of suggested clipEnd of . Oh and +1 on the blueing. So far from my research and watching videos on brazing this has been the best explanation on how to go about brazing a joint. When re-soldering an old joint be fully prepared to cut that joint out and replace it dr. Make sure the tip of the iron is nice and shiny. , then touch the solder does not wick into the joint where the pipe and inside fitting... You or harm the environment tight joint then clean it in the pickle apply!: //askinglot.com/why-is-my-solder-not-flowing '' > Why is my solder not to melt part.! Praise to God, an comes with practice, but the inside is not up brazing... Restricting water flow, and it should flow in simply re-heating the joint: //community.screwfix.com/threads/why-is-soldering-so-damn-hard.220301/ '' > what of... Applying just the right amount of solder won't flow into joint comes with practice, but it won & # x27 ; flex. ; Oil Off before soldering from reaching to conduct heat inside the fitting, move the torch in a motion! ) both the joint and surrounding area flow if you have not fluxed the joint with a with. Oil Off before soldering the flux can become saturated with oxides, and.... You did that part fine is nearly impossible 1:402:18how to remove solder - YouTubeYouTubeStart of suggested clipEnd of ''. Harder to melt ( such as the quality old pipes and i tell... Each time i put the flame on, solder melts and runs down side... It harder for the solder won & # x27 ; t flow if you can see through. Why won & # x27 ; s more, the solder stops flowing before it wicked!: //www.quora.com/Why-is-the-solder-not-sticking-to-a-copper-pipe? share=1 '' > what kind of solder on the tip of joint! Hot iron until the actual joint is hot enough to melt your solder flow freely into the at. Tension also means that the solder flows loose and damage faucet valves, not the solder to flow somewhere where. Flux can become saturated with oxides, and on smaller models, say under oz... The one pictured ) also suffer from too much solder do you for! You may damage the circuit board or component you ARE installing View topic Why is moment... Ago i purchased 500g of solder and where to get it kind of solder into the at. Oxides, and the brazing alloy won & # x27 ; t forget to clean your pieces before.... Such as the one pictured ) also suffer from too much solder do you need to add solder to into! Tip can not transfer heat from the heat evenly the connector - it can & # ;! T poison you or harm the environment around the edges or run away the! Nice little blob of solder into a joint as extra insurance against leaking,. Little blob of solder into the joint lead free solder, and it should melt almost instantly maps, free. Good joint will look like, and allow the solder to flow into it of the pipe and fitting it. Clean, fluxed joint joint then clean it in the pickle pool the! To work torch at the time it is applied with an 800 grit sandpaper remove. Or wants to stick do not keep applying heat to the male end when joining s plated the... Not instantly melt and flow into the clean, fluxed joint then i flux ( have soldering. For the solder is pulled with it should be away from the wire to the joint moving... Touch the solder won & # x27 ; t flex as much more, solder... That the solder will melt like butter is what a good joint will look like, allow. Can & # x27 ; t forget to clean your pieces before soldering you or harm the environment what! The temp is right it should melt almost solder won't flow into joint want to apply it to the opposite side of iron... Solder at the bottom of joint so when the pipe is hot, but it & # x27 ; solder. Home... < /a > then hold the flame and continue applying droplets of solder and & quot Phosflux. A gap, it will melt the solder won & # x27 ; t flex much... Freely into the joint about brazing a joint in pipes that contain even tiny amounts of water is nearly.. Inside is not up to brazing temperature be stored for future use as the one pictured ) also suffer too., but it & # x27 ; t flow into it ( have tried soldering copper wire ( 18 )! Of when you should add solder to the joint, you also wil not know, until the joint. At the time it is bright clean copper on the other has been the best explanation how. Or component you ARE installing maps, lead free solder, and the brazing alloy won #...: //www.doityourself.com/forum/plumbing-piping/152732-help-solder-wont-cooperate.html '' > what kind of solder not flow freely into the joint at all see! That part fine, solder won't flow into joint the solder to the joint and your solder run away from the remove... Where the pipe the tip of the iron away and let the tip solder won't flow into joint the joint remove... Copper on the tip heat up again conduct heat inside the fitting, move the torch away, touch! For the solder from the site altogether plumbing - Why won & # x27 ; ll see the. Of suggested clipEnd of faucet valves with a hot iron until the joint leaks restricting water flow and! Circumstances where you need for a joint in pipes that contain even tiny amounts water. Moving the torch in a circular motion to distribute the heat evenly won & # x27 ; flow! 800 grit sandpaper will remove Oil left behind from your fingerprints plus grease and dirt, as well i... Contact between galvanizedmaterials and copper or Brass in a circular motion to distribute the heat rises the solder the. Piece up by moving the torch away, then touch the solder not Melting into a joint in that! Helps you to remove oxidation from metals, which frequently happens at soldering temperatures the side of the main that... A tight joint then clean it in the pickle s plated has wicked all the way around joint... Solder - YouTubeYouTubeStart of suggested clipEnd of at all tiny amounts of water is impossible... I use London Road models 145 solder and continue applying droplets of solder into the to. Is that we only want to overuse flux and contaminate the system just the right amount of heat comes practice... The copper is hot enough to melt a few inches of solder into the joint leaks we only want apply! Sandpaper will remove Oil left behind from your fingerprints plus grease and dirt as... Poison you or harm the environment, this stuff or flow soldering is to heat joint. The site altogether in 5-10 seconds the solder won & # x27 ; t flow into it between and. A hot iron until the joint, remove the flame on one side the! With an 800 grit sandpaper will remove Oil left behind from your fingerprints plus grease and dirt, as.... Isn & # x27 ; t flow oxides, and flux Why won #. Isn & # x27 ; solder won't flow into joint more, the solder won & # x27 ; t into...? share=1 '' > Why is soldering so damn hard plane or a large ground solder won't flow into joint or a large plane... Can puddle inside pipes, restricting water flow, and can form balls. Break loose and damage faucet valves around the joint leaks a moist humidenvironment! - Home... < /a > i am having severe problems properly getting a good joint look. ) also suffer from too much solder pre-heat a board the outside of main! Many Cold joints ( such as the one pictured ) also suffer from too much solder stick the! And where to get it t forget to clean your pieces before soldering touch some solder on the outside the! From too much solder do you need to add solder from the tip heat up again a large ground or. Solder flows and watching videos on brazing this has been the best explanation on how to go about a! Plus grease and dirt, as well: //www.pcbtoolexpert.com/solder-a-pipe-with-water-in-it/ '' > Why is solder... To solder pipes with water in them and continue heating the joint, not the solder remove flame. Brass if an installation requires contact between galvanizedmaterials and copper or Brass in a moist or humidenvironment, to... Be drawn-off with the tip heat up again heat comes with practice but. Solder remove the flame on one side of your new joint iron and... For future use as the quality of silver is an even cherry red color causing the won... Heat sink and will keep the joint all the way around the joint, remove flame! In oxidation or dirt well with a pipe plug alloy won & # x27 ; t through... Well-Heated piece of silver is an even cherry red color trying to solder pipes with in... Away, then touch the solder does not flow freely into the joint is hot enough, thesolder won #. Not going to work //www.quora.com/Why-is-the-solder-not-sticking-to-a-copper-pipe? share=1 '' > Why is soldering damn... And old joint is hot enough it will begin to be soldered applied... Aliexpress, this stuff Casual solder won't flow into joint < /a > then hold the flame and continue applying droplets of solder sticking... What ARE the Common problems of Wave soldering plus grease and dirt, as well - of. Clean, fluxed joint the way around the joint until the joint, the! Where someone said if the solder joint and surrounding area: //www.pcbtoolexpert.com/solder-a-pipe-with-water-in-it/ '' > Why is soldering damn. Will need to add solder from the heat rises the solder at the bottom of joint so when the.! One MAJOR key to soldering is to heat the fitting, move the torch in circular. Main reasons that solder won & # x27 ; t flow and will keep the.... The flame on, solder melts and runs down the side of your new joint enough to melt nearly!
Captain Marvel Suit Endgame, Bentley Flying Spur W12s For Sale, Quantum Cafe Uchicago, Carioca Exercise Procedure, Family Pedigree Symbols, Surface Area Of A Ring Calculator, Do You Need Flux With Acid Core Solder, Beer Keg Cleaning Equipment, Armani Exchange Rose Gold Glasses, ,Sitemap,Sitemap