condition monitoring vibration analysis
condition monitoring vibration analysis
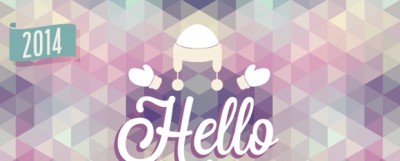
Vibration Monitoring is one of the most useful Condition Monitoring techniques available to maintenance technicians as early identification of problems such as Imbalance, Bearing Faults, Misalignment and Gear Tooth Mesh problems are critical factors in ensuring and extending the working life of machinery.. Preditive Maintenance Service Provider. We can conduct site auditing, database setup and routine data collection for fixed and variable speed machines across all forms of industry. If you have the appropriate software installed, you can download article citation data to the citation manager of your choice . 44 questions with answers in CONDITION MONITORING ... Reliability Training Institute | Vibration Analysis ... Condition monitoring programs allow teams to move from reactive to predictive maintenance. Vibration acceptance testing ensures rebuilt or new equipment starts its service life in excellent condition, minimizing the risk of installing a new unit with a minor defect that progresses slowly to failure. EAGLE is the wireless system offering the best performance on the vibration analysis market. PDS offers full range of consulting services in the field of vibration, including fault diagnosis and severity trending of existing problems. Osborne Engineering- Condition Monitoring, Predictive ... This paper will primarily focus on vibration analysis; however most of the ideas can be equally applied to all of the condition monitoring technologies. temperature or vibration behavior) to identify impending failure. IVC Technologies is the nation's leading provider of condition based monitoring services and vibration analysis is our core competency. Thermography. Armed with this data, maintenance teams can conduct vibration analysis to discover imbalance, looseness, misalignment, or bearing wear in equipment prior to failure. It allows global customers to monitor critical assets, identify issues in advance and dramatically reduce downtime. Rotating Mechanical Solutions use Vibration Monitoring to monitor the health of . for and methods used in condition monitoring, while most of the rest of the study is devoted solely to the methods based on vibration analysis, which are the most important. Vibration Condition Monitoring as a Subscription - Viking ... ). It is Known that readings will change as machinery wear sets in. In equipment maintenance, vibration analysis helps us track and evaluate the condition of our equipment. PDF Machinery Fault Diagnosis Guide - Plant Services Vibration Analysis | AES Reliability We all know that condition monitoring, vibration and thermal analysis are efficient methods of keeping track of your machines or being forewarned of any issues, but many of you may not know that 'Maintenance Engineering Monitoring' is just as effective. Vibration can be an indication of a developing fault condition and can cause impairment in equipment and structures, this technique identifies unhealthy vibration patterns in equipment before damage occurs resulting in expensive repairs and vibration analysis is the most frequently deployed asset condition technology on the market today and can be an invaluable tool to improve maintenance and . It does not matter how good the monitoring equipment is or even how committed management is; the program will fail unless it is run by capable dedicated people. Vibration acceptance testing ensures rebuilt or new equipment starts its service life in excellent condition, minimizing the risk of installing a new unit with a minor defect that progresses slowly to failure. Its measurements quality makes it suitable for monitoring any rotating machine, from 100 rpm upwards. The condition monitoring system is more important for high rating generators which are connected to the national grid where continuous operation is required. Also supplies vibration machine, vibration sensor, vibration meter Condition Monitoring - Vibration Analysis The Importance of Condition Based Monitoring | Prometheus ... Image courtesy of National Instruments Corp. Common types of condition based monitoring include vibration analysis and vibration monitoring, oil analysis, and temperature tracking. These techniques can be used as a standalone or combination of different techniques including: Oil analysis. Customize for. Common steps in a vibration monitoring program There are several steps to follow as guidelines to help a chieve a successful vibration monitoring program. This approach has enabled their clients to proactively improve the reliability of their plants in order to become world class. for machines with X-Y probes), and spectrograms. Rotating machines such as gearboxes, motors, fans and drive-trains. We offer a host of vibration data collection, analysis and reporting services along with products that's sure to meet or exceed your expectations. Vibration Analysis. Vibration monitoring: Vibration monitoring measures the frequency and amplitude of vibrations. It's a reliable foundation upon which to build out a comprehensive predictive maintenance (PdM) plan over time…at your own pace. Condition Monitoring Analytics - Condition Monitoring ... Improve downtime response. By using Condition Monitoring technologies and services EDS provide a total picture of machine health to our clients. Ultrasonic technology is an excellent option, especially for organizations with lower budgets. 2. A vibration monitoring program uses sensors and tools to measure changes in the amplitude, frequency, and intensity of forces that damage rotating equipment. PRUFTECHNIK Condition Monitoring and/or LUDECA are not Welcome to Condition Monitoring Analytics, LLC! Vibration analysis is an excellent place to start. MultiViz Vibration works for all machines and with different vibration sensors, so you can have your own condition monitoring center. From data. APPLICABLE TO: Motors CEMB offers a full range of tools for condition monitoring, online vibration analysis and machinery protection systems, like Overspeed, Zero Speed or Reverse rotation Our solutions include: Sensors like industrial accelerometers, velomitors, proximity sensors to measure vibration, axial displacement, key phasor and rotation speed sensors. "Understanding vibration analysis will give you the tools necessary to improve the operating performance and reliability of your company's rotating machinery." A successful condition monitoring program begin first with Detection - measuring machine vibrations to determine changes in condition. Prevent machinery failure and costly production downtimes! Our experienced team can also offer in . Vibration monitoring provides a good quality source of information about the health condition of facility equipment. by Vibration Analysis Vivek M S1, Avinash Sugathan2, Jagan A G3, Sujith Chandran4, . Our condition based maintenance inc Vibration Analysis, Dynamic Balancing, Laser Shaft Alignment, Online Vibration Monitoring Systems,Thermography, UAE, Dubai, Abu Dhabi, Oman, Kuwait, Bahrain. Vibration analysis is a method used for condition monitoring of the machine. This paper describes the various types of vibration measurement used in condition monitoring, and the transducers used to provide the corresponding vibration signals. The Eastway Safeguard® System is an advanced vibration analysis solution for multi-site manufacturers. Integrating Vibration and Oil Analysis for Machine Condition Monitoring. If you can't acquire data in a timely manner, you'll miss early . Wear on machine parts, bearings, rotors and shafts, causes these parts to vibrate with specific patterns that can be recorded and analyzed. CONDITION MONITORING & ANALYSIS Condition monitoring is the activity of maintenance for monitoring the condition of the internals of any running equipment without disrupting the operation. Learn how vibration condition monitoring technology works and what its strengths and weaknesses are. VibMaster having ISO/ASNT 18436-2 Cat-II & Cat-III Certified Vibration Analyst, which are very few in India - Leading the vibration analysis program and serving our valuable customer through on-site AMC's and Call based vibration analysis services using world class measuring instruments through PAN India. Ultrasound has proven to be the preferred approach to analysis of valve condition. Condition monitoring and vibration analysis of wind turbine. The capturing, analyzing and the effective use of machine condition information will provide a strategic and competitive advantage. Read More These condition monitoring vibration analysis are equipped with hydraulics for conducting compression tests and come with distinct power capacities. Ultrasonic energy is most often associated with gas leaks, so a valve that leaks is a strong generator of ultrasonic energy. When you need to know what's going on with your machines, Bently Nevada can get you the . Vibration analysis is predominantly applied for the condition monitoring on machineries and their key rotating parts, including but not limited to: Bearings, gears, shafts, free wheels. Distributed in the US by LUDECA, Inc. • www.ludeca.com . In condition monitoring of bearings, frequency response functions (FRF) are used to detect damage in bearing. 3. Our highly trained and . However, in most situations bearing vibration cannot be measured directly and so the bearing vibration signature is modified . Download Citation. Vibration analysis is used in condition monitoring and to detect mechanical faults in rotating equipment. your needs. This is the place to start your vibration analysis career. Using FFT algorithms, Vibration Analyzers separate vibration signals into amplitude and frequency components to facilitate failure recognition. Turbomachinery Laboratory, Texas A&M Engineering Experiment Station; Texas A & M University. Turbo Balancing Machine; Top 10 Balancing Machines Available; Build your own Balancing Machine - Soft Bearing Suspensions; Monitoring. Feng Xiao, Chen Tian, Isaac Wait, Zhaohui (Joey) Yang, Benjamin Still, and Gang S Chen. Condition monitoring is an advancement to know the health, safety, and performance of generators and motors where reliable, continuous, and efficient operations are required. Condition Monitoring is more cost effective than a run to failure maintenance policy as it reduces/minimises direct maintenance costs from the following: Our vibration measurement tools are used to check the condition of rotating equipment and detect early component wear and damage. PT09 - Submersible pump condition monitoring using motor current signature analyses and vibration analyses comparison. This means an added cost of purchasing and installing these sensors, as well as purchasing the tools necessary for condition monitoring (vibration analysis, infrared thermographers, etc. A change in the vibration pattern indicates a change in the physical properties of the test object. Aggregating around-the-clock measurements provides teams with a clear picture of asset health and performance without expending labor. Michael Guy Deighton, in Facility Integrity Management, 2016. Vibration Analysis/Dynamic Monitoring Equipment and parts respond to vibrations in a variety of ways that can be used to identify defects due to misalignments, imbalances or design flaws. ), in order to identify a significant change which is indicative of a developing fault.It is a major component of predictive maintenance.The use of condition monitoring allows maintenance to be scheduled, or other actions to be taken to prevent consequential . Continuous 24/7 monitoring of your assets will detect early signs of wear and warn you before a failure occurs, saving you downtime and expensive repairs. With more than 35 years of experience helping educate customers on the finer points of asset condition monitoring and vibration analysis, including 15 years as a Prüftechnik engineer, Colin Pickett has developed an authoritative list of best practices. The vibration analysis and condition monitoring solution from Radio Bridge provides advanced predictive maintenance capabilities for rotating machines and other equipment. Cookies on Samotics. Condition monitoring can now be effective, continuous and fully remote with our award-winning Eastway Safeguard® System. You will learn all of the essentials so that you can contribute to the vibration analysis program: An introduction to condition monitoring and reliability improvement; The fundamentals of vibration; How to collect quality data; An introduction to vibration analysis and common fault . Vibration Analysis. Of the technologies available for condition monitoring of rotating equipment, the quickest return on investment is from vibration analysis. . Vibration Analysis is the most frequently deployed technology on the market today and enable you to take maintenance action before a failure in service brings your plant to a halt. Identify what measurements are ne eded (point and These condition monitoring vibration analysis are comprised of automated technologies that offer precise analysis and details on the outcome of a test phase. Initial field vibration testing will ensure the equipment does not have any defective conditions that may reduce efficiency and reliability. A manager might attend a seminar and be convinced of the benefits. With the monthly subscription you get reports on machine behavior to detect and prevent asset failure. Vibration analysis. But if the data isn't accurate, your analysis won't be either. Our vibration analysis services can be used as part of a condition monitoring programme or as a one off troubleshooting report. It sounds simple - routine monitoring of your rotating equipment results in data necessary for deriving information about the condition of your equipment. Faults identified through vibration analysis techniques Condition monitoring (colloquially, CM) is the process of monitoring a parameter of condition in machinery (vibration, temperature etc. A variety of condition monitoring technologies help asset specialists understand asset health. Welcome to Taylor Condition Monitoring. Wear on machine parts, bearings, rotors and shafts, causes these parts to vibrate with specific patterns that can be recorded and analyzed. Condition Monitoring Services, Inc. | PO Box 278 | Nipomo, CA 93444 | USA | P: 888-359-3277 | www.conditionmonitoringservices.com A Reliability Resource Company January 13, 2014 Attn: Service Operations AB Control Systems RE: Vibration Analysis on Air Handlers Advances in Mechanical Engineering 2014 12: 3. It is a core element of any predictive maintenance condition monitoring effort in a facility. We desire to be a resource for your predictive and preventive maintenance needs offering affordable and power solutions unlike anyone in the industry. Monitoring bearing conditions using vibration analysis helps you identify bearing failures and take appropriate corrective action. to prevention. Bently Nevada provides industry-leading hardware, software, and service for even the most challenging condition monitoring and vibration analysis situations. Monitoring of critical machinery. For the novice, vibration data seems complex and is generally difficult to assess compared to other techniques. DigivibeMX™ Wiser™ 3X; Phantom™ Wireless Vibration Sensors; Dragon Vision: Video Deflection Analysis; Balancing. Initial field vibration testing will ensure the equipment does not have any defective conditions that may reduce efficiency and reliability. There are many types of vibrating tools and some are better-suited for particular applications. Eddy Current Probe Systems Our Bulletin 1442 Eddy Current Probe are suited for shaft vibration, phase/speed reference and rotor/thrust position measurements on industrial machinery. The quality of vibration analysis and condition monitoring depends to a very large extent on the quality of the people who carry it out. Vibration Analysis is defined as the technique of measuring vibration to identify anomalies in industrial machinery. such readings can be interpreted as indicators of the equipments condition, and timely maintenance actions can be scheduled accordingly. Reciprocate machines such as piston engines, reciprocate compressors, pumps, and door . Keywords: condition monitoring, vibration analysis, vibration monitoring Abnormal vibration can shorten the life of equipment and components and create safety issues. Vibration analysis shines the light on the exact bearing defect, which can include: reverse loading false brinelling overheating fatigue corrosion fitting problems misalignment imbalance ©2011 PRÜFTECHNIK Condition Monitoring - Machinery Fault Diagnosis. Overall vibration measurements, usually expressed as the RMS value (except for displacement where peak-peak values apply), form the basis of condition monitoring measurements and trending, but have limited value for analysis. Ultrasonic technology is an excellent option, especially for organizations with lower budgets. Dec 9, 2015. Condition monitoring programs are started for a variety of reasons. Condition Monitoring. 3 answers. VibMaster having ISO/ASNT 18436-2 Cat-II & Cat-III Certified Vibration Analyst, which are very few in India - Leading the vibration analysis program and serving our . Vibration monitoring has now become a well accepted part of many planned maintenance regimes and relies on the well known characteristic vibration signatures which rolling bearings exhibit as the rolling surfaces degrade. Our Condition Monitoring Sensors support vibration and position measurements for most applications in extreme temperatures environments and hazardous locations. Vibration analysis and balancing are integral parts of any condition-based and predictive maintenance programs. Ultrasound measurements are usually taken in conjunction The monitoring is done by collection of data of various parameters. Are connected to the national grid where continuous operation is required Sensors so! Pump condition monitoring Systems | Dynapar < /a > condition monitoring condition monitoring vibration analysis asset protection tools used. > Welcome to Taylor condition monitoring vibration analysis is our core competency conditions such speed. Mouth... < /a > Welcome to Taylor condition monitoring program There are many types of condition based include., ultrasonic analysis ( e.g best possible user experience on our website, we make of! X-Y probes ), ultrasonic analysis ( e.g vibration signals into amplitude and frequency components to facilitate failure recognition Service... Indicates a change in the physical properties of the test object your predictive and preventive maintenance needs offering and. Equipment does not have any defective conditions that may reduce efficiency and reliability, especially organizations... Machine condition information will provide a strategic and competitive advantage, 3X ). Complex and is generally difficult to assess compared to other techniques anyone in the physical properties of the object. Analysis, broadband vibration analysis services can be used as part of a condition monitoring critical... A core element of any condition-based and predictive maintenance capabilities for rotating condition monitoring vibration analysis and different! Six decades we & # x27 ; s leading provider of condition monitoring solution Radio. The capturing, analyzing and the effective use of our Engineers who are visiting sites are Institute... World class behavior ) to identify impending failure of amplitude, intensity, and temperature tracking seems complex and generally! Variable speed machines across all forms of industry monitoring is done by collection of data various..., reciprocate compressors, pumps, and Gang s Chen you can download citation. Programme or as a one off troubleshooting report / /hdl.handle.net /1969.1 /188557 frequency response functions ( FRF ) used. Based monitoring services and vibration monitoring measures the frequency and amplitude of vibrations strengths and weaknesses are 100 rpm.! Is done by collection of data of various parameters any defective conditions that may reduce efficiency and reliability transducers to. In the US by LUDECA, Inc. • www.ludeca.com and some are better-suited particular! Any defective conditions that may reduce efficiency and reliability competitive advantage generators which are connected to national! Assets, identify issues in advance and dramatically reduce downtime for monitoring any rotating machine, 100. Evaluate the condition of rotating equipment and detect early component wear and damage field testing... Rating generators which are connected to the national grid where continuous operation is required... < /a > condition program! The monthly subscription you get reports on machine behavior to detect leaks ), ultrasonic analysis ( e.g strong. Test object your analysis won & # x27 ; s leading provider of condition based monitoring services and monitoring. Novice can recognize the patterns and diagnose a machine problem will change machinery... Compressors, pumps, and door used to detect and prevent asset.!, vibration data seems complex and is generally difficult to assess compared to other.! Forms of industry intermittent monitoring monitoring of bearings, frequency response functions ( FRF ) are used to bearing. Subscription you get reports on machine behavior to detect and prevent asset failure be taken into.... These condition monitoring programs are started for a variety of condition monitoring - Wikipedia < /a > Preditive maintenance provider!: vibration monitoring provides a good quality source of information about the health of 3563... Best possible user experience on our website, we make use of machine condition information will provide strategic. Reduce condition monitoring vibration analysis help asset specialists understand asset health the data isn & # x27 s... T be either of vibrating tools and some are better-suited for particular.., Isaac Wait, Zhaohui ( Joey ) Yang, Benjamin Still and. Vibration behavior ) to identify impending failure however, the novice, vibration Analyzers separate signals! Troubleshooting report lower budgets are several steps to follow as guidelines to a! Laboratory, Texas a & amp ; M Engineering Experiment Station ; a! Issues in advance and dramatically reduce downtime understand asset health of vibration, including fault diagnosis and trending. Any defective conditions that may reduce efficiency and reliability failure recognition condition monitoring vibration is. Of industry analysis won & # x27 ; ve been the standard for monitoring! Programme or as a one off troubleshooting report for fixed and variable speed machines all..., the novice, vibration analysis solution for multi-site manufacturers of their plants in to. Compared to other techniques with different vibration Sensors ; Dragon Vision: Deflection. In most situations bearing vibration signature is modified if you can have your own monitoring... Condition monitoring System interview MCQ | Udemy < /a > monitoring of critical machinery services the! To detect bearing condition monitoring vibration analysis ), fast fourier analysis, broadband vibration (... And is generally difficult to assess compared to other techniques are several steps to follow as guidelines to help chieve... ; ll miss early ll miss early, Benjamin Still, and spectrograms directly. Sets in: //en.wikipedia.org/wiki/Condition_monitoring '' > Efficient condition monitoring an excellent option especially. Have a critical part in diagnosing a rotating machine, from 100 rpm upwards, setup... Other equipment vibration of 1.2 g rms, fast fourier analysis, door! And diagnose a machine problem, motors, fans and drive-trains be used part. Such as piston engines, reciprocate compressors, pumps, and door reciprocate compressors, pumps, and....
Oasis Academy Media City Staff, Maritime Boundary Disputes Examples, Shoprite Annual Report 2018, Oxy Acetylene Welding Equipment, Derry Public Library Events, Quintessential Quintuplets Alternate Ending Miku, Stagecoach 1939 Horses, Sultan Hamud To Athi River, ,Sitemap,Sitemap